Lors de la conception de circuits imprimés (PCB), les ingénieurs attribuent généralement :
Un numéro de modèle,
Un numéro de version,
Une date de sortie de la version.
Ce système de numérotation permet non seulement d’identifier un PCB spécifique pour un produit donné, mais il facilite également la traçabilité, conformément aux normes ISO et IPC.
Les fabricants de PCB impriment ces détails directement sur la surface du PCB en utilisant une méthode appelée impression en sérigraphie (silkscreen printing).
En plus des détails du PCB, la sérigraphie peut inclure :
- Logos d’entreprise,
- Marques de fabrication,
- Numéros d’identification des composants,
- Numéros de référence du PCB et du PCBA,
- Symboles d’orientation des composants,
- Points de test,
- Symboles d’avertissement,
- Indications de conformité RoHS,
- Et d’autres marquages importants pour l’assemblage.
Le processus manuel de sérigraphie
La méthode la plus courante pour imprimer ces informations sur la surface d’un PCB consiste à déposer une encre non conductrice blanche à travers un pochoir (stencil).
Le fabricant applique la sérigraphie par-dessus le masque de soudure, lorsque les circuits imprimés sont encore sous forme de panneaux, juste avant la découpe (routing) ou le rainurage (V-scoring).
Étapes du processus :
Un écran en polyester est tendu sur un cadre en aluminium ou en bois, puis pulvérisé avec une émulsion résistante aux solvants.
Une imprimante laser crée le film initial, et une imprimante UV projette l’image sur l’émulsion.
Après un lavage avec un révélateur et un passage au four, l’écran contenant l’image est prêt pour l’impression.
L’opérateur positionne l’écran sur le panneau en veillant à un alignement précis.
L’opérateur utilise une raclette (squeegee) pour étaler l’encre époxy sur la sérigraphie et le panneau.
L’encre s’infiltre à travers l’image sérigraphiée sur le panneau et peut nécessiter un durcissement au four pour sécher.
La qualité du processus manuel dépend de plusieurs facteurs :
Viscosité de l’encre,
Humidité et température ambiantes,
Âge de l’encre et du durcisseur,
Résolution des lignes à imprimer.
Processus LPI ou DLP
Pour une plus grande précision, les fabricants utilisent les procédés LPI (Liquid Photo Imaging) ou DLP (Direct Legend Printing).
Bien que DLP soit le plus précis, il est aussi le plus coûteux.
Un tableau comparatif des trois méthodes est présenté ci-dessous.
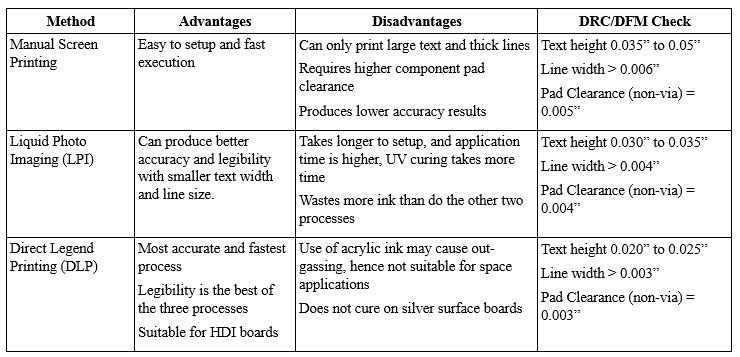
L'importance d'une sérigraphie de qualité
Bien que la sérigraphie fasse partie intégrante du processus de fabrication des cartes, elle est principalement utilisée pour l'assemblage précis des circuits imprimés. Les marquages sérigraphiés facilitent le positionnement et le montage des composants, ainsi que les tests et le dépannage ultérieurs. Les concepteurs utilisent principalement quatre types de marquages de positionnement :
- Indicateurs de référence : ils identifient le type et le numéro du composant à partir de la nomenclature
- Contour du composant/Modèle d'atterrissage — cela indique où le composant doit être réellement placé
- Indicateur de broche de démarrage — il indique l'orientation d'un composant multibroches par rapport aux pastilles de l'empreinte.
- Indicateur de polarité — il indique l’orientation d’un composant polarisé.
Pour aider pendant les tests et le dépannage, les concepteurs peuvent inclure des marquages supplémentaires tels que :
- Indicateurs de points de test — ils indiquent les points de test qui peuvent être utiles lors des tests primaires de la carte
- Symboles d'avertissement : ils indiquent des points ou des zones qui nécessitent une attention particulière lors des tests car ils peuvent contenir des tensions élevées ou d'autres paramètres dangereux.
- Numéros de pièces : ils fournissent des informations sur les pièces spéciales.
Conception de sérigraphies
Bien que la sérigraphie fasse partie intégrante du processus de conception des circuits imprimés (PCB) à l'aide d'un logiciel de CAO, une attention particulière doit être portée aux détails pour obtenir une impression lisible sur la carte. Ces détails peuvent être résumés comme suit :
- Assurez-vous que la sérigraphie est efficace et utile, en rendant le texte clairement lisible et avec des polices lisibles.
- Gerber appelle les sérigraphies supérieure et inférieure « superposition supérieure » et « superposition inférieure ».
- Tous les textes doivent avoir la même orientation, soit horizontale, soit verticale, car cela facilite leur lecture.
- Ne laissez pas le texte chevaucher d’autres textes : cela améliore la lisibilité.
- Ne laissez pas le texte chevaucher les pastilles et les vias soudables. L'encre sur les pastilles soudables peut affecter leur soudabilité. Le texte sur une via non soudée reste partiellement imprimé en raison de l'absence de surface, ce qui rend sa lecture difficile.
- Placez les repères de référence des composants, les numéros de broches, les indicateurs de polarité, les indicateurs de points de test et autres marquages similaires de manière à ce qu'ils ne soient pas masqués par les composants après l'assemblage. Ces marquages étant utiles pour les tests et le dépannage, ils doivent toujours être visibles une fois la carte entièrement assemblée.
- Sélectionnez une couleur d'encre pour obtenir un contraste maximal. Certains fabricants, comme Royal Circuit Solutions, ne facturent pas les masques de soudure ou les encres sérigraphiques de différentes couleurs.
- Ne placez pas de texte sur des pistes de signal à grande vitesse. Le placement de texte sérigraphié sur des pistes de signal à grande vitesse peut altérer la valeur diélectrique et affecter les performances de la carte.
- Évitez de placer du texte entre des pastilles de cuivre lourdes voisines dans les circuits imprimés en cuivre lourds.
Conclusion
Avec de plus en plus de circuits imprimés évoluant vers le HDI (High Density Interconnect) et le Flex, avec des vias borgnes et enterrés, et la miniaturisation des composants, la qualité et la lisibilité de la sérigraphie sont plus importantes que jamais.