L'IPC a récemment publié une mise à jour de l'IPC-6012. La révision F couvre les spécifications de qualification et de performance des circuits imprimés rigides. Vous trouverez ci-dessous quelques-unes des modifications importantes apportées par cette révision et leur impact potentiel sur la conception et la fabrication des circuits imprimés.
En règle générale, les documents IPC ne fournissent pas de contexte sur les raisons des modifications, ni sur leurs causes et leurs effets. Dans ce document de référence, Summit présente les modifications et leur impact sur les PCB afin d'aider l'industrie à mieux comprendre les avantages de la dernière révision et à comprendre comment et pourquoi ces changements sont nécessaires.
______________________________________________________________________________________________________________________________
Révision F Nouvelle section 1.4.3
Profondeur de perçage arrière
La nouvelle section 1.4.3 a été ajoutée pour clarifier l'endroit où une mesure de contre-perçage est évaluée lorsque la profondeur de contre-perçage est spécifiée. Cela était nécessaire car le point de départ du contre-perçage pouvait être considéré comme spécifié dans la section 1.4.2, ou il aurait pu être considéré au niveau de la feuille de départ ou de l'épaisseur totale du cuivre. Avec la nouvelle section, la mesure est claire et ne prend pas en compte le cuivre de surface pour valider la profondeur.
Summit recommande que le foret arrière soit spécifié en utilisant les attributs de la figure 1-1 et toutes les notes 1 à 6.
- Considérations de conception lorsqu'une conception comporte des forets arrière dans des trous plaqués.
- Spécifiez le côté à percer et la couche à ne pas couper (MNC).
- Vérifiez la distance de conception entre le diamètre du foret arrière et les conducteurs adjacents au chemin du foret arrière.
- Créez un programme de perçage distinct pour chaque type/portée de perçage arrière.
- Créez un tableau de perçage et spécifiez le perçage arrière, le diamètre avec le nombre.
- Précisez si le trou plaqué à percer doit être rempli d'époxy ou non.
- Précisez si le foret arrière doit être rempli d'époxy après le forage arrière.
- Spécifiez la longueur du tronçon autorisée.
- Indiquez clairement si le foret arrière doit être plaqué et fixé à un plan de masse externe. Indiquez également si le fabricant de PCB doit modifier les données pour obtenir un remplissage de masse en cuivre fini sur le foret arrière.
- Notez également que certaines imperfections du cuivre sur le foret arrière rempli d'époxy sont autorisées conformément aux sections 3.3.1, 3.3.9, 3.6.2.19 et 3.6.2.20 de l'IPC-6012.
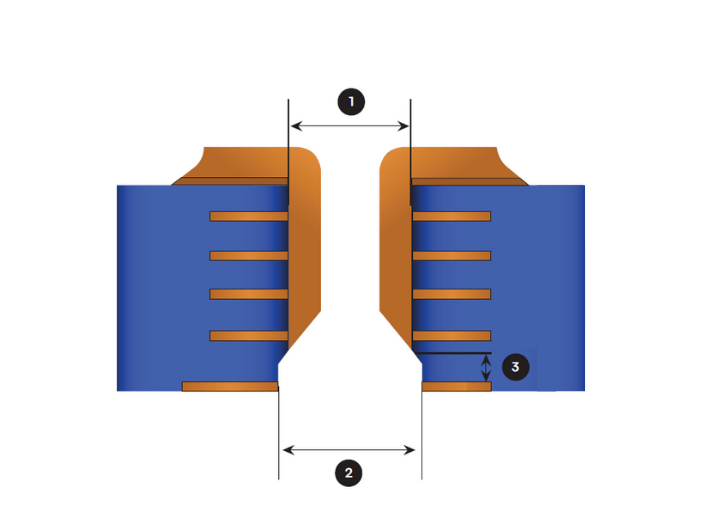
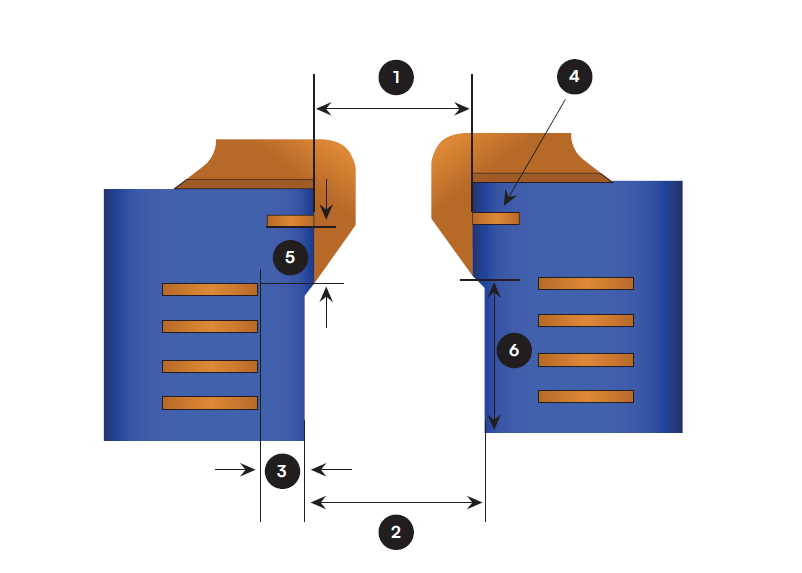
______________________________________________________________________________________________________________________________
Révision F Section 3.6.2.14.1
Couches internes plaquées
Cette section est nouvelle dans le document de base, mais faisait en fait partie de l'IPC-6012 AM1 (Amendement 1), qui a été publié en mars 2022. Il est important de comprendre que cette section n'est en fait pas une modification mais une clarification des exigences relatives à une couche plaquée interne. Avant l'amendement, il n'était pas clair si la couche plaquée interne devait être traitée selon les règles relatives aux couches externes et suivre le tableau « Épaisseur du conducteur externe du circuit imprimé fini après placage » (le tableau était le tableau 3-15 dans l'IPC-6012 rev E, et est maintenant le tableau 3-18 révision F) ou si l'évaluation devait suivre le tableau « Épaisseur de cuivre de la couche interne après traitement » (tableau 3-14 de la révision E et maintenant dans la révision F tableau 3-17). Il n'était pas clair quelle règle devait être utilisée, ce qui créait de la confusion et d'éventuels rejets de pièces si la règle externe devait être utilisée à la place de la règle d'épaisseur interne.
Ce fut pendant de nombreuses années un débat intense et difficile au sein du comité IPC jusqu'à ce que la règle soit finalement clarifiée avec la section 3.6.2.14.1.
Section 3.6.2.14.1 Couches internes plaquées – Lorsque les couches internes sont plaquées, l'épaisseur totale minimale (feuille de cuivre plus placage de cuivre) doit être conforme au tableau 3-17 (il s'agit du tableau d'épaisseur de cuivre de la couche interne). La feuille de cuivre minimale spécifiée doit être utilisée avant le placage. Lorsque le conducteur fini global est spécifié en termes de poids plutôt que d'épaisseur, l'épaisseur minimale du conducteur après placage doit être l'épaisseur minimale après traitement du tableau 3-17 pour ce poids de cuivre particulier. L'épaisseur de la feuille de cuivre initiale utilisée avant le placage peut être réduite à un maximum de 50 % de l'épaisseur minimale après traitement (tableau 3-17). L'absence de feuille de cuivre au niveau du coude du trou due au traitement ne doit pas être considérée comme un motif de rejet, à condition que le placage par enroulement minimal sur la feuille soit présent. Toutes les autres exigences de placage (par exemple, placage par enroulement ou par recouvrement) doivent être respectées et peuvent être incluses dans la mesure finale de l'épaisseur totale.
La nouvelle section précise que la couche de placage interne suivra l'exigence de cuivre total inférieure trouvée dans le tableau 3-17 plus le placage enveloppant et le placage de capuchon si nécessaire. Pour le concepteur/ingénieur PCB qui a accepté cette règle, il n'y a aucun changement. Pour les ingénieurs qui s'appuyaient sur l'épaisseur des conducteurs externes du tableau 3-18, il existe une inquiétude que le conducteur puisse être beaucoup plus fin.
Par exemple, si un dessin de fabrication fait mention d'une demi-once sur une couche plaquée interne qui a une voie borgne se terminant sur la couche, nous suivrons le tableau 3-17 épaisseur minimale de 11,4 µm [.000449”] plus placage d'enveloppement minimum de 5 µm[0 .000197] ce qui équivaudrait à 16,4 µm[0 .000646”] .
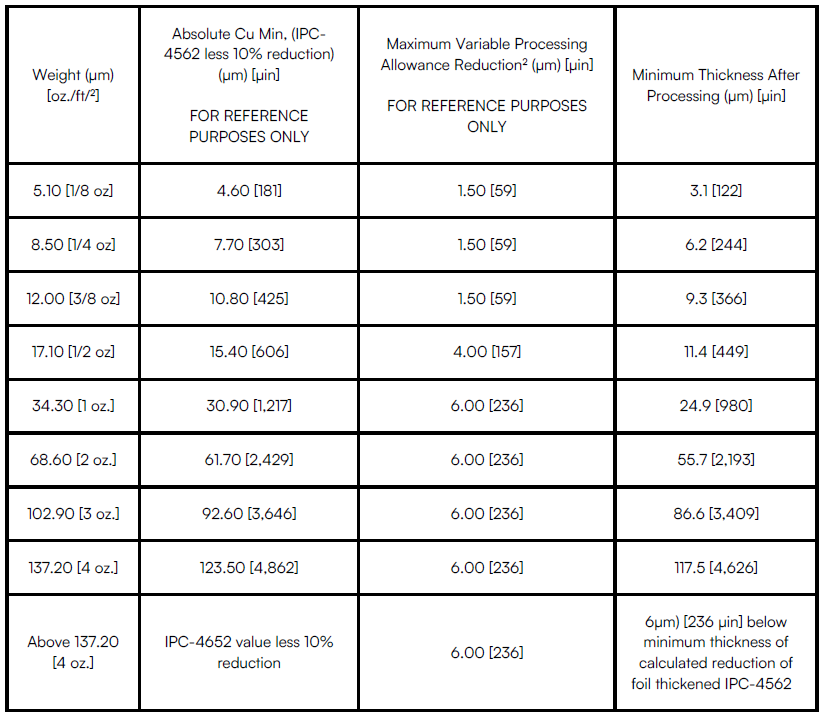
Pour ceux qui utilisaient auparavant la règle de la couche externe, ils s'attendaient à ce que l'épaisseur totale pour la classe 3 soit de 38,4 µm[0 .001512] .
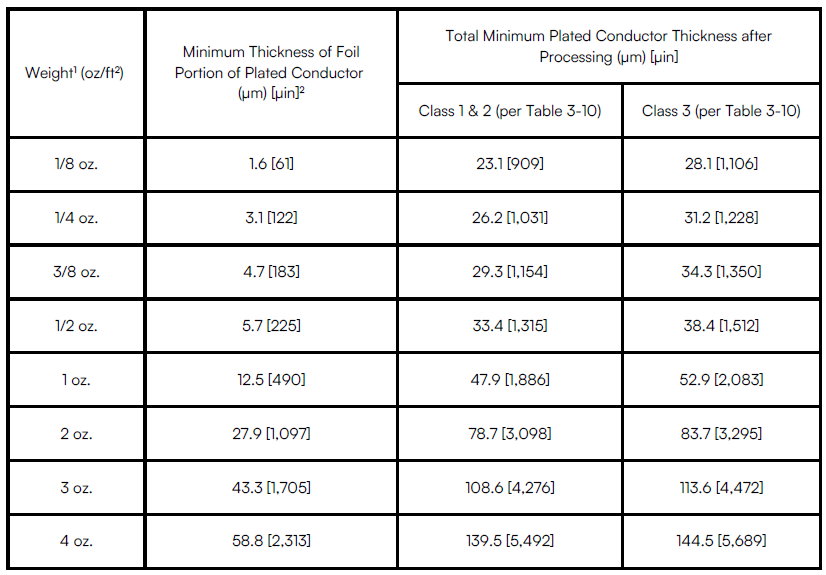
La différence est de 22µm[0 .000866”] ce qui est significatif.
De plus, cette section souligne une autre règle qui doit être prise en compte lors de la conception lorsque le dessin spécifie l'épaisseur de la couche de cuivre comme épaisseur finie.
Lorsque le conducteur fini global est spécifié en termes de poids plutôt que d'épaisseur, l'épaisseur minimale du conducteur après placage doit être l'épaisseur minimale après traitement du tableau 3-17 pour ce poids de cuivre particulier .
Lorsque l'impression spécifie l'épaisseur finie en fonction du poids, le tableau 3-17 est en vigueur, qui correspond à la hauteur totale la plus basse du conducteur. En règle générale, la couche extérieure présente des trous de placage finaux qui ajouteront environ une once de cuivre à la surface de la couche extérieure, ce qui égalera ou dépassera les exigences du tableau externe 3-18. Cependant, s'il n'y a pas de trous de placage finaux et que l'impression indique le poids de cuivre fini au lieu du poids de départ, il n'est pas nécessaire d'ajouter à la feuille de départ au-delà des exigences de placage d'enveloppement et de capuchon selon l'IPC-6012. Le concepteur doit prendre en compte chaque fois que la feuille de cuivre est spécifiée comme finie en onces. Veuillez noter que le cuivre est considéré comme une épaisseur de départ à moins que le document n'indique fini.
Avantages de la section 3.6.2.14.1
- Les règles d'acceptation pour une couche interne plaquée sont désormais claires. Il y a eu des cas où le fabricant a appliqué la règle actuelle, mais les cartes ont été rejetées lorsque l'utilisateur final a appliqué l'épaisseur du conducteur pour une couche externe.
- En autorisant une épaisseur de conducteur plus fine pour une couche plaquée, les fabricants peuvent planifier des empilements avec des diélectriques plus fins et éviter le délaminage ou les vides de laminage. À mesure que l'épaisseur du cuivre augmente, le risque d'arrêt du verre ou de manque de résine entre les couches plaquées internes augmente.
- Un cuivre total plus fin réduira la variation du conducteur, ce qui permettra des performances de signal plus cohérentes.
- Réduit l'épaisseur globale du PCB grâce à une épaisseur de conducteur inférieure et à la réduction du préimprégné entre les couches internes plaquées.
- Élargit les possibilités de conception. Permet une plus grande gamme de conducteurs d'impédance.
Considérations
- Les concepteurs doivent calculer l'épaisseur minimale du cuivre en fonction de l'épaisseur interne du cuivre conformément au tableau 3-17.
- Utilisez l'épaisseur du conducteur fini en fonction de la valeur d'épaisseur réelle et non en onces.
- Tenir compte des conceptions plus anciennes qui pourraient entraîner une épaisseur de couche interne plaquée plus faible. Les fabricants pourraient commencer à cibler les critères d'acceptation désormais « clarifiés ».
______________________________________________________________________________________________________________________________
Section 3.6.2.6.2 Pénétration du cuivre.
Nouvelle définition pour l'évaluation de la gravure en retour.
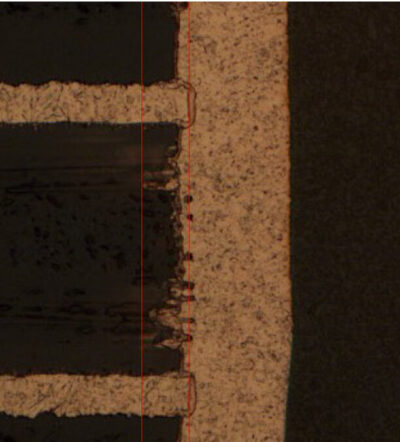
Brève explication de Etch Back.
La gravure en creux désigne le retrait contrôlé du matériau diélectrique autour du trou métallisé pendant le processus de fabrication. Ce procédé est considéré comme crucial pour une bonne adhérence du placage aux parois internes du trou. L'évaluation consiste à évaluer la profondeur et l'uniformité de la gravure en creux afin de garantir une adhérence solide et uniforme du matériau au substrat. Une gravure en creux correcte est essentielle pour minimiser la perte de signal, garantir de bonnes performances électriques et favoriser la fiabilité globale du circuit imprimé. Des techniques d'évaluation précises, telles que l'analyse transversale et l'inspection optique, sont utilisées pour vérifier que la gravure en creux répond aux exigences spécifiées, contribuant ainsi à la fonctionnalité et à la longévité des appareils électroniques.
La gravure en retour d'un trou percé est une condition requise par les documents d'approvisionnement. Le traitement de la gravure en retour peut s'avérer complexe pour tous ceux qui ont dû planifier, fabriquer ou évaluer cette gravure. L'obtention de ces conditions est limitée et, par le passé, la définition de son évaluation était difficile à transmettre et à évaluer.
Dans les révisions précédentes de la norme IPC-6012, nous avons utilisé des images d'un trou gravé et indiqué où la mesure commence, c'est-à-dire là où le tampon percé est le plus loin dans le trou après la gravure, et où se trouve l'autre extrémité. L'autre extrémité est basée sur ce qui a été défini comme « l'élimination diélectrique », qui est le résultat de l'effet de mèche, de déchirures aléatoires du foret ou de gougeage du foret et du nettoyage du trou. Avec l'ancienne définition, il est difficile de déterminer où le matériau stratifié n'est plus fracturé à partir du processus de perçage ou du traitement du trou. C'est là que la nouvelle définition de la pénétration du cuivre vient à la rescousse.
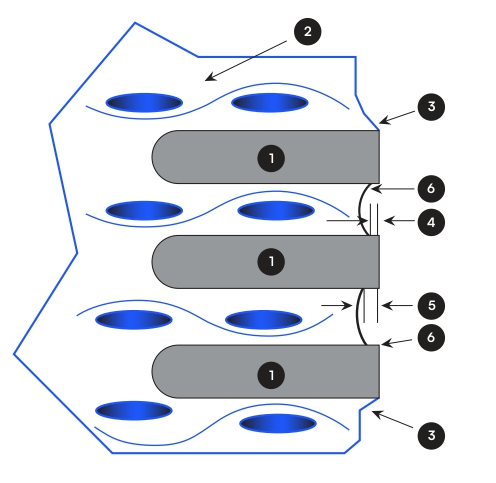
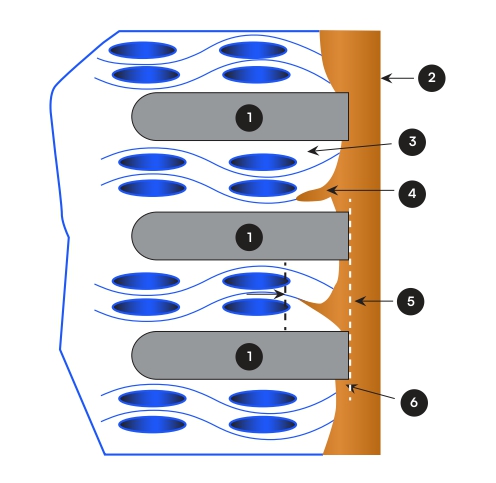
L'évaluation de la gravure arrière est désormais définie comme « Pénétration totale du cuivre ». La tolérance de mesure est essentiellement la même que celle de l'IPC-6012 rev E, sauf que la mesure s'étend désormais du bord percé de la feuille de couche interne jusqu'à la pénétration du placage de cuivre. Le tableau 3-8 est utilisé pour déterminer la pénétration maximale du cuivre autorisée par classe. L'IPC-6012 réf F a simplifié l'évaluation en éliminant les définitions compliquées de ce qu'est l'enlèvement dans une évaluation de section transversale. La tolérance de pénétration du cuivre est la valeur combinée de la tolérance de gravure maximale plus l'effet de mèche maximal basé sur le tableau 3-8. Exemple d'un état d'impression Gravure arrière 5 µm-38 µm[0 .0002”-0.0015”] et le tableau 3-8 La tolérance de classe 3 indique 80 µm[0 .00315”] alors la tolérance maximale de pénétration du cuivre est de 38 µm maximum pour la gravure arrière[0 .0015” + maximum wicking 80µm[0.00315] = maximum 118 µm[0 .0046”] L'évaluation de la gravure consiste désormais simplement à mesurer la pénétration du cuivre et à confirmer que la pénétration la plus éloignée ne dépasse pas 118 µm.[0 .0046”] .
Pénétration du cuivre (voir figure 3-18) | La pénétration totale du cuivre ne doit pas dépasser la somme des deux 125 µm[4,921 µin] tolérance maximale d'absorption plus tolérance maximale de gravure ou d'élimination des bavures | La pénétration totale du cuivre ne doit pas dépasser la somme des deux 100 µm[3,937 µin] tolérance maximale d'absorption plus tolérance maximale de gravure ou d'élimination des bavures | La pénétration totale du cuivre ne doit pas dépasser la somme des deux 80 µm[3,150 µin] tolérance maximale d'absorption plus tolérance maximale de gravure ou d'élimination des bavures |
En quoi la nouvelle règle est-elle utile ? Grâce à cette nouvelle définition claire, un fabricant qui gère et contrôle la gravure à la valeur minimale autorisée bénéficie de tolérances pour l'effet de mèche pouvant se produire lors du perçage d'un trou métallisé. Tous les matériaux ne se valent pas : certains, notamment le polyimide, présentent un effet de mèche plus important que d'autres. En gérant la gravure à un minimum de 5 µm,[0 .0002”] lorsque le maximum autorisé pour la gravure arrière est de 80 µm[0 .00315”] Le produit fini permettrait un retrait plus important du stratifié, puisque l'évaluation porte sur la pénétration totale du cuivre. Cette nouvelle définition clarifie l'évaluation et n'a pas réellement modifié l'état final du trou métallisé défini dans la norme IPC-6012 rév. E.
Considérations :
- Formation des techniciens de laboratoire pour évaluer la pénétration totale du cuivre et non la gravure et l'effet de mèche en tant qu'évaluations autonomes.
- Formation des inspecteurs de sources pour comprendre que les rapports de laboratoire ne mesureront que la pénétration du cuivre et non plus l'élimination totale.
- L'évaluation de l'effet de mèche de l'addendum spatial IPC-6012, révision F, actuellement à l'étude, ne constituera potentiellement plus une violation autonome de l'effet de mèche. Restez à l'écoute des développements concernant l'addendum spatial. Je vous tiendrai au courant dès que la modification aura été acceptée.
______________________________________________________________________________________________________________________________
Section 3.3.10 Cavités de la carte imprimée
La révision F de l'IPC-6012 introduit enfin de nouvelles règles concernant spécifiquement l'incorporation de cavités dans les conceptions de circuits imprimés. Les nouvelles règles reflètent la nature dynamique de la fabrication électronique et la demande croissante de solutions innovantes dans diverses industries. En établissant de nouvelles règles et en affinant les exigences existantes, la révision F de l'IPC-6012 s'efforce d'établir une nouvelle norme pour les processus de conception et de fabrication, offrant aux ingénieurs et aux fabricants des directives plus claires pour s'orienter dans les complexités associées à l'incorporation de cavités dans les circuits imprimés modernes.
Dans cette nouvelle section vous constaterez que 3 types ont été définis :
- Type 1 Aucune métallisation sur le sol ou les murs creux.
- Type 2 Métallisation sur un ou plusieurs murs, ou sur le sol, mais pas les deux.
- Métallisation de type 3 sur le sol de la cavité et les murs adjacents avec placage continu.
Les cavités doivent répondre aux exigences dimensionnelles de la conception. Il est important que les tolérances dimensionnelles standard pour un profil de PCB soient utilisées pour une dimension X et Y de cavité. Il est également important de garder à l'esprit que le même système CNC qui fraise le profil d'un PCB est utilisé pour réaliser une ouverture de cavité. Une tolérance de profondeur doit également être indiquée. Il est recommandé de prévoir une tolérance de profondeur de +/- 0,005 po. Les profondeurs doivent être basées sur les points de départ de la couche extérieure et non sur une couche ou un diélectrique particulier.
Le type 1 est simplement une poche fraisée dans un PCB qui permet de placer les composants à l'envers (bug mort) tout en ayant des fils qui peuvent toujours être soudés à la surface de la couche externe.
Conditions d'une cavité de type 1
- Le sol de la cavité doit avoir une apparence visuellement uniforme.
- L'exposition des fibres perturbées doit être conforme à la section 3.3.2.6 de l'IPC-6012. (oui, le verre tissé sera perturbé si nous fraisons dans le stratifié. Il faut s'y attendre.)
- Lors de l'utilisation de matériaux préimprégnés/liants prédécoupés dans une cavité, un espace non laminé peut se produire en raison d'un mauvais alignement du matériau. Cet espace est autorisé à partir de la paroi de la cavité jusqu'à 50 % de la distance au conducteur le plus proche de la paroi de la cavité ou 0,010 pouce, la valeur la plus faible étant retenue.
Le type 2 correspond généralement à une cavité permettant la pose d'une plage de connexion par fil ou le placement d'un composant dans une cavité sur la couche interne souhaitée. Dans ce cas, les parois latérales de la cavité sont non métallisées. Le type 2 permet la connexion directe des composants à la couche interne souhaitée. Cette application offre une meilleure intégrité du signal. L'utilisation de cette méthode présente des limites et des préoccupations concernant les applications de soudure et de masque de soudure. Les masques de soudure ne sont pas conçus pour être appliqués sur une couche interne de sous-stratification, puis soumis à un cycle de laminage. L'adhérence et l'aspect du masque de soudure fini peuvent ne pas répondre aux exigences de la norme IPC-6012 3.7 Exigences relatives aux masques de soudure . Il est fortement recommandé de revoir votre conception avec Summit si une conception de type 2 est requise.
Conditions d'une cavité de type 2 :
- Pour les conducteurs de cavité continus dans le plan, dépassant de la paroi de la cavité, le flux d'adhésif est autorisé jusqu'à 0,75 mm[0 .0295”] sur les caractéristiques du conducteur. Il s'agit de la même valeur que celle trouvée dans la norme IPC-6018.
- Pour les terrains sur le plancher de la cavité qui empiètent de 0,75 mm[0 .0295”] À partir du mur creux, la marge de colle doit être conforme aux normes AABUS. Si cette condition est constatée, une vérification avec un fabricant est nécessaire. Dans le cas contraire, la résine risque de couler sur une plage soudable.
- Lors de l'utilisation de matériaux préimprégnés/liants prédécoupés dans une cavité, un espace non laminé peut se produire en raison d'un mauvais alignement du matériau. Ceci permet de séparer la paroi de la cavité jusqu'à 50 % de la distance entre la paroi et le conducteur le plus proche, ou 0,010 pouce, la valeur la plus faible étant retenue.
Pour les cavités de type 2 et 3, les dispositions suivantes s'appliquent :
- Sauf indication contraire dans la documentation d'approvisionnement, les zones vierges des éléments conducteurs sur le sol d'une cavité nécessitent des finitions soudables ou connectables par fil, à l'exclusion de la zone de flux d'adhésif autorisée, définie par la zone centrale de 60 % du contour de l'élément (rond, rectangle, carré, etc.) et doivent répondre aux exigences de fabrication de 3.5.4.
- Pour les cavités de type 2 à parois plaquées et de type 3, lors d'un examen visuel effectué conformément à la section 3.3, les vides de placage et de revêtement dans les parois de la cavité ne doivent pas dépasser la valeur autorisée par le tableau 3-6 (nouveau dans la révision F). Chaque paroi latérale des cavités plaquées doit être évaluée individuellement. La surface cumulée de plusieurs vides sur une même paroi ne doit pas dépasser les pourcentages de surface.
Matériel | Classe 1 | Classe 2 | Classe 3 |
---|---|---|---|
Cuivre | Jusqu'à 20 % de la surface du flanc peut être vide. Les vides ne doivent pas dépasser 60 % de la longueur ou de la profondeur du flanc. | Jusqu'à 10 % de la surface des parois latérales peut être vide. Les vides ne doivent pas dépasser 40 % de la longueur ou de la profondeur des parois latérales. | Jusqu'à 5 % de la surface des parois latérales peut être vide. Les vides ne doivent pas dépasser 20 % de la longueur ou de la profondeur des parois latérales. |
Revêtement de finition* | Jusqu'à 20 % de la surface du flanc peut être vide. Les vides ne doivent pas dépasser 60 % de la longueur ou de la profondeur du flanc. | Jusqu'à 10 % de la surface des parois latérales peut être vide. Les vides ne doivent pas dépasser 40 % de la longueur ou de la profondeur des parois latérales. | Jusqu'à 5 % de la surface des parois latérales peut être vide. Les vides ne doivent pas dépasser 20 % de la longueur ou de la profondeur des parois latérales. |
* Remarque 1. Les bords des interruptions intentionnelles de placage des bords ne doivent pas nécessairement avoir de revêtements de finition finaux (c'est-à-dire que le cuivre exposé est autorisé dans ces zones).
Considérations de conception
- Les perçages à proximité des cavités doivent respecter les règles relatives aux éléments situés sur le bord du circuit imprimé. Les conducteurs doivent être à 0,020 pouce des bords de la cavité. Ce phénomène est fréquent dans les conceptions de cavités : les éléments sont placés trop près du bord et peuvent entraîner un rejet de la conception pour la fabrication. Un positionnement trop proche du bord peut nuire aux rendements de fabrication. Si votre conception comporte des éléments proches du bord de la cavité, il est préférable de la vérifier avec Summit.
- Les trous métallisés à l'extérieur de la paroi de la cavité doivent être retirés d'au moins 0,030" du bord de la cavité.
- Les vias dans la cavité d'écoulement doivent être plaqués, remplis et recouverts d'un revêtement de protection conformément à la norme IPC-4761 Type VII. Ces vias ne doivent pas être ouverts.
- Le masque de soudure sur les sols des cavités doit être évité et, si nécessaire, peut ne pas répondre aux exigences du masque de soudure fini selon la section 3.7.
- Passez en revue les exigences de finition de surface dans la zone de cavité avec Summit.
- Les rendements des PCB à cavité peuvent être affectés par les exigences de traitement.
- Les temps de rotation sont plus longs pour les circuits imprimés à cavité et augmentent en fonction du nombre de cavités requises.
______________________________________________________________________________________________________________________________
Section 3.3.1 Placage des bords Nouveau paragraphe ajouté aux bords
Nouveau paragraphe :
Lorsque le placage des bords d'une carte imprimée est spécifié, les règles suivantes s'appliquent :
La séparation du placage des ancrages internes (voir IPC-2228) le long du bord plaqué est interdite. Un décollement de la paroi du bord par rapport au diélectrique est acceptable, à condition que toutes les exigences dimensionnelles soient respectées. Les vides de placage ne doivent pas dépasser trois emplacements sur le périmètre du bord plaqué et 1,27 mm.[0 .050in] Quelle que soit la longueur. Les nodules sur les bords plaqués sont acceptables, à condition qu'ils ne soient pas lâches et qu'ils respectent les dimensions globales du circuit imprimé. Le cuivre nu exposé est autorisé sur les bords des languettes de rupture (traitement) après le fraisage final du profil. Les bavures métalliques au niveau des languettes de rupture (traitement) sont acceptables, à condition qu'elles ne soient pas lâches et/ou n'affectent pas l'ajustement et la fonction. L'enroulement des bords plaqués sur la surface doit respecter les dimensions indiquées dans la section 3.5.1.
Les documents IPC-6012 révision F et IPC-2228, publiés en octobre 2022, sont les premiers documents IPC à traiter des exigences de conception et de performance des circuits imprimés à bords plaqués. L'IPC-2228 constitue un excellent guide pour la conception de circuits imprimés à bords plaqués. Voir la section 6.4 de l'IPC-2228.
Voici quelques considérations sur la conception des bords plaqués :
- Enrobage du cuivre. Le cuivrage des bords du circuit imprimé présente une très faible résistance au pelage. La résistance élevée au pelage de la couche externe de cuivre d'un circuit imprimé classique est obtenue grâce aux revêtements appliqués sur la feuille de cuivre, qui favorisent l'adhérence entre le préimprégné et la feuille de cuivre. Un bord plaqué du circuit imprimé est fraisé/défoncé à l'aide d'une fraise, ce qui laisse une surface lisse, presque polie. Cette surface lisse est recouverte de cuivre autocatalytique et ne bénéficie d'aucun promoteur d'adhérence. Enrobage du cuivre sur la surface de la couche externe, on bénéficiera des promoteurs d'adhérence de la feuille de cuivre qui fixent le haut et le bas du placage des bords. Le placage des bords peut facilement se décoller si la conception ne comporte pas de placage enrobage. Il est recommandé d'envelopper les surfaces supérieure et inférieure de 0,63 mm.[0 .025”] . Bien que cette valeur semble élevée, gardez à l'esprit que le profil de la plupart des PCB est de 0,254 mm[0 .010] , et dans le pire des cas, il est bénéfique d'enrouler correctement le cuivre sur la couche extérieure de cuivre.
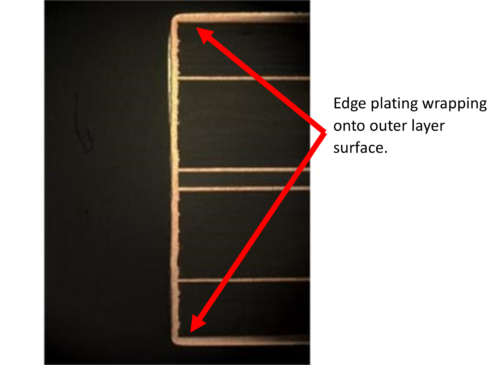
- Prolongez le cuivre jusqu'au bord du circuit imprimé. L'adhérence du placage des bords peut être améliorée en prolongeant le cuivre au-delà du bord du circuit imprimé. Le cuivre sera exposé lors de l'opération de fraisage/routage à l'endroit où le placage des bords est souhaité. Le cuivre exposé servira d'ancrage au placage des bords, réduisant ainsi le risque d'arrachement.
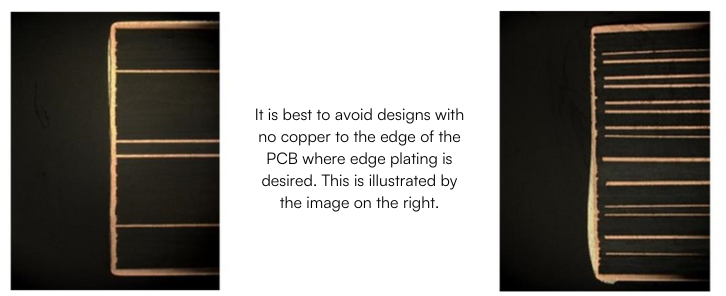
Voici un exemple exagéré de décollement du placage des bords.
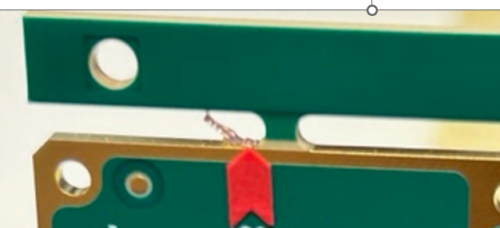
- Le placage des bords ne doit être connecté qu'au réseau de terre. Il est essentiel de retirer le cuivre de toutes les autres couches où un placage des bords est souhaité.
- Retirez tout le cuivre sur toutes les couches pour les bords non plaqués, incluez la tolérance de démarcation autorisée.
- Prévoyez une tolérance de démarcation généreuse entre les bords plaqués et non plaqués du circuit imprimé. Cette démarcation est créée par une opération de fraisage/défonçage. Comme la broche tourne (à grande vitesse), la plongée de la fraise est relativement nette, mais l'arrachement peut arracher le placage de bord, peu résistant au pelage. Ces arrachements peuvent aller de la position cible à une traction supplémentaire de 0,020 pouce et une perte de placage de bord sur le côté du circuit imprimé. Voir l'exemple ci-dessous.
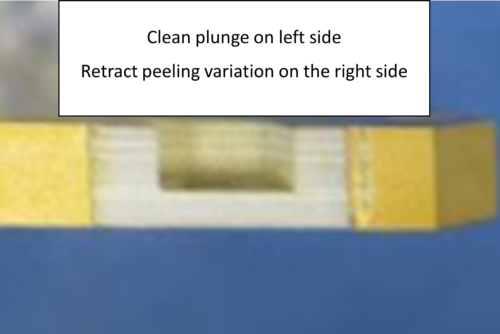
Considérations :
- Comprendre les règles relatives au placage des bords dans la section 6.4 de l'IPC-2228 (publiée en octobre 2022).
- Prévoir des tolérances dimensionnelles généreuses pour la démarcation de la transition entre le bord non plaqué et le bord plaqué. La démarcation/transition n'est pas exacte. Une précision de démarcation de +/- 0,025 po serait avantageuse.
- Étendez uniquement le cuivre pour les couches de terre et retirez toutes les autres couches.
- Pour les bords non plaqués, retirez le cuivre sur toutes les couches.
- Indiquez dans votre documentation d'approvisionnement que le cuivre jusqu'au bord du PCB est prévu par la conception.
- Le placage des bords doit être utilisé pour le blindage de la terre et non comme conducteur. La précision de la position et de la longueur n'est pas pratique.
______________________________________________________________________________________________________________________________
Tableau 1-2 Exigences par défaut
Le tableau 1-2 par défaut de l'IPC-6012 est souvent négligé ou méconnu, mais il figure dans toutes les spécifications de performance IPC-6012, IPC-6013 et IPC-6018. Il fournit les tolérances du fabricant pour le traitement et la fabrication d'un circuit imprimé lorsque les documents d'approvisionnement ne précisent pas les exigences relatives aux attributs suivants.
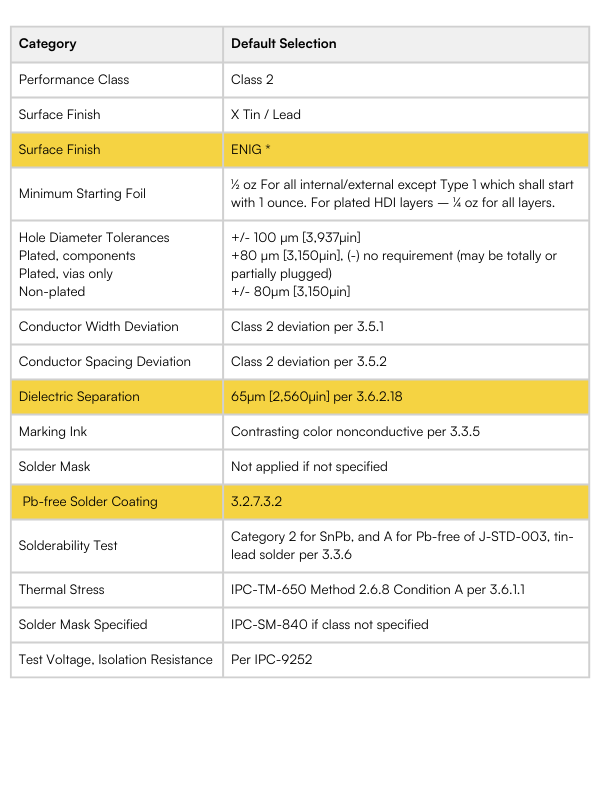
Les nouveaux changements dans le tableau 1-2 sont surlignés en JAUNE.
En règle générale, les documents IPC ne fournissent pas de contexte sur les raisons des modifications, ni sur leurs causes et leurs effets. Summit, grâce à cette série de billets de blog, a partagé ces changements et leur impact sur les PCB afin d'aider l'industrie à mieux comprendre les avantages de la dernière révision et à comprendre comment et pourquoi ces changements sont nécessaires.
Voici un bref résumé des trois changements et de la manière dont ils se sont produits.
Finition de surface ENIG.
Avec l'utilisation courante de l'ENIG plutôt que des finitions étain/plomb, les fabricants utilisent de moins en moins de finitions étain/plomb. Il n'est pas rare de voir le traitement de l'ENIG réalisé en interne, tandis que celui de l'étain/plomb est sous-traité à un prestataire externe. De plus, l'utilisation d'un système de nivellement de soudure à air chaud HASL peut engendrer des coûts d'électricité de plus de 25 000 $ par mois. La finition de surface ENIG offre également une surface coplanaire uniforme, avantageuse pour l'assemblage de composants CMS. Cette nouvelle modification a une date limite d'utilisation. Toutes les versions initiales d'un plan continueront de suivre l'ancienne règle de l'étain/plomb uniquement lorsqu'une finition de surface n'est pas spécifiée. À compter des dates de publication initiales sur le plan du 1er octobre 2023, lorsqu'une finition n'est pas spécifiée, le fabricant pourra utiliser un revêtement de soudure ENIG, étain/plomb ou sans plomb (autre modification du tableau 1-2). Cela permettra au fabricant de choisir la finition la plus économique et la plus efficace parmi les trois finitions répertoriées dans le tableau 1-2.
Séparation diélectrique
Le diélectrique minimum a une nouvelle valeur par défaut inférieure de 65 um[2,560u”] . Ce nouveau changement permettra aux fabricants de prendre des décisions concernant l'épaisseur diélectrique des diélectriques percés HDI/Laser sans demander une épaisseur inférieure à l'allocation minimale des révisions précédentes de 90 µm[3,543u”] . La plupart des diélectriques microvia utilisent des épaisseurs nominales comprises entre 75 µm et 100 µm[3,000u”-4,000u”] Cette plage nominale serait soit contraire à l'ancien minimum, soit irrémédiablement non conforme. Ce nouveau changement empêchera la suspension de tâches dans le processus d'ingénierie initiale, ou les demandes de dérogation sur le produit fini pour permettre une valeur diélectrique minimale inférieure.
Soudure revêtue sans plomb
Les fabricants pourront utiliser un revêtement de soudure sans plomb si la finition de surface n'est pas spécifiée. Cela réduira la nécessité d'avoir des systèmes HASL fonctionnant à la fois avec des systèmes sans étain/plomb et sans plomb dans la même usine.
Considérations :
- La finition de surface par défaut proposera désormais plusieurs options. Si ces options doivent être contrôlées, il sera nécessaire de spécifier la finition de surface dans les documents d'approvisionnement entrants.
- Les minimums diélectriques seront plus bas et les tensions de résistance devront être revues dans les conceptions haute tension.
- L'utilisation d'un revêtement de soudure sans plomb peut entraîner des incompatibilités de soudure.
______________________________________________________________________________________________________________________________
Section 3.6.2.6.1 Preuve de gravure en creux
Preuve de gravure (si spécifiée) Lorsque seule une preuve de gravure (c'est-à-dire une preuve visuelle de l'enlèvement latéral de résine et/ou de fibres de verre) est spécifiée dans la documentation d'approvisionnement, pas plus de deux couches par trou ne doivent présenter de gravure nulle. Toutes les autres couches doivent avoir une gravure supérieure à zéro.
Il s’agit d’une nouvelle section qui a été ajoutée à la section 3.6.2.6, et il est très important de la comprendre et de l’appliquer correctement.
Lorsque la documentation d'approvisionnement autorise la preuve de la gravure en creux, il est possible de ne pas avoir de preuve de gravure en creux sur plus de 2 couches. Cette nouvelle règle est utile pour les trous à rapport hauteur/largeur élevé supérieur à 10:1 et ayant des trous percés de petit diamètre, généralement de 0,25 mm[0 .010”] ou moins. Pour ces trous de petit diamètre, il est difficile d'obtenir des traces de gravure au centre du trou et cela a un impact sur les rendements. La nouvelle règle permet que 2 couches au milieu d'un trou métallisé ne présentent aucune trace de gravure. Ce changement sera très bénéfique pour améliorer les rendements de fabrication.
Les essais de refusion et de choc thermique des trous métallisés via les méthodes IPC-TM-650 2.6.27 et 2.6.7.2 avec gravure en retour, preuve de gravure en retour ou absence de gravure en retour ont démontré la capacité de passer la refusion et les chocs thermiques. Ces résultats soutiennent cette tolérance dans cette révision de l'IPC-6012 rév. F.
Lors de l'application de la règle, il doit y avoir des couches internes qui montrent des preuves, mais dans le cas d'empilements avec plus de 4 couches, cette règle est appliquée lorsque des preuves de gravure en arrière sont spécifiées.
Vous trouverez ci-dessous un exemple de rapport hauteur/largeur de 12:1 avec 1 couche sans trace de gravure. Rejeté dans la norme IPC-6012 rév. E et désormais acceptable dans la norme IPC-6012 rév. F. Veuillez noter qu'une formation à l'inspection à la source sera nécessaire pour une évaluation correcte de cette section.
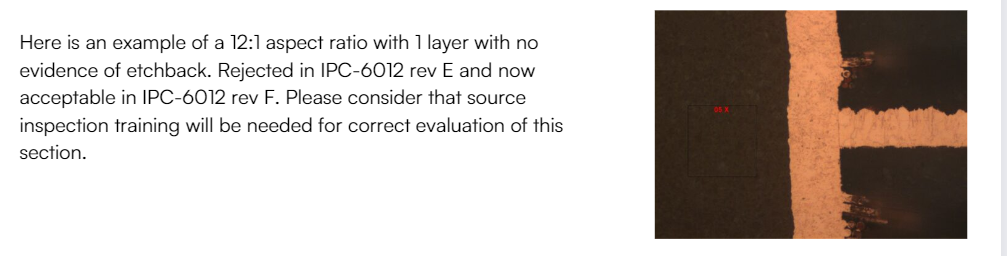
______________________________________________________________________________________________________________________________
Section 3.6.2.18.1 Espacement diélectrique minimal
Si le diélectrique minimum n'est pas spécifié, un nouvel espacement diélectrique minimum entrera en vigueur pour les dessins dont la date de publication initiale est postérieure au 31 décembre 2023. La nouvelle règle qui entrera en vigueur le 1/1/2024 aura un minimum de 65 um[0 .00256”] lorsque le diélectrique minimum n'est pas spécifié. Pour les conceptions publiées avant la date limite, l'ancienne règle du diélectrique minimum restera en vigueur pour ces conceptions. Le diélectrique minimum avant la date limite était de 90 µm[0 .003543”] et le restera en raison de la date limite du 31/12/2023.
Alors pourquoi ce changement ? Microvias
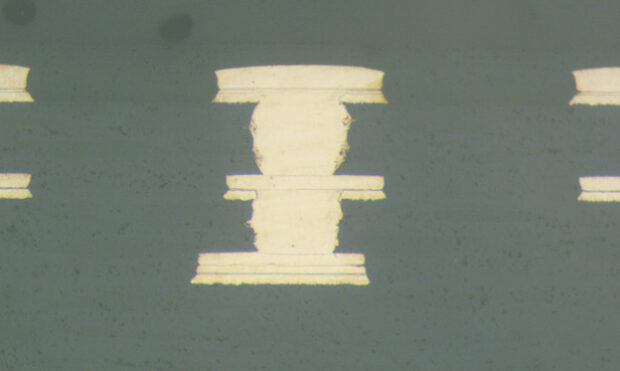
Les empilements de microvias typiques cibleront un diélectrique compris entre 60 µm et 100 µm[0 .0025” to 0.004”] Pour gérer le rapport d'aspect des microvias. Si une conception HDI ne spécifie pas de diélectrique minimal pour la plage attendue, le circuit imprimé fini peut facilement mesurer en dessous de l'épaisseur minimale précédemment autorisée de 90 µm.[0 .003543”] Pour éviter les retards et le rejet de pièces nécessitant une résistance minimale inférieure, les fabricants doivent demander un nouveau diélectrique minimal autorisé pour l'expédition du produit fini. Les nouvelles conceptions ne subiront plus ce risque de retard.
Après le 31/12/2023, les nouvelles conceptions HDI initiales pourront être planifiées et mises en production sans nécessiter de nouveau diélectrique minimal. Cette nouvelle règle réduira les délais de demande d'AABUS (accord entre l'utilisateur et le fournisseur) pour un produit fini ou une nouvelle conception en phase de planification.
Considérations :
- Cette règle s'applique uniquement si la sortie initiale est postérieure au 31/12/2023.
- Toutes les conceptions dont la sortie initiale est prévue avant le 1/1/2024 suivront l'ancienne règle.
- L'épaisseur et la coupe des dattes sont indiquées dans la section 3.6.2.18.1 de l'IPC-6012 rév. F.
- Ceci ne s’applique pas aux modifications de révision.
- Une formation à l’inspection des sources sera nécessaire pour une évaluation correcte de cette section.
______________________________________________________________________________________________________________________________
IPC-6012 révision E section 3.6.2.11.3 – Fossettes et saillies
Les bosses et les saillies des microvias ne sont plus des AABUS. Le deuxième paragraphe de la section 3.6.2.11.3 de la révision E de l'IPC-6012 commençait par « Les exigences relatives aux saillies (bosses) ou aux dépressions (fossettes) dans les microvias borgnes remplis de cuivre doivent être des AABUS.
La révision F comporte désormais un nouveau tableau 3-14 (3-14 n'est plus le tableau pour l'épaisseur de la feuille de couche interne après traitement). Le tableau 3-14 est désormais intitulé « Dépression et saillie dans les microvias remplis de cuivre ».
Diamètre du trou conçu | supérieur à 0,15 mm [0 .006 in] | inférieur ou égal à 0,15 mm [0 .006 in] |
---|---|---|
Rempli par dépression (fossette) - Maximum | 50 µm [1,969 µin] | 25 µm [984 µin] |
Rempli par saillie (bosse) - Maximum | 25 µm [984 µin] | 25 µm [984 µin] |
Remarque 1 : S'applique aux microvias dans les plages destinées à être soudées lors de l'assemblage.
Ce qui est intéressant avec cet ajout, c'est que le tableau n'utilise pas de classes mais est décomposé par diamètres de vias laser. La tolérance de dépression/alvéole est de 25 µm/0,000984" pour une microvia inférieure ou égale à 0,15 mm/0,006", et si elle est supérieure, la dépression/alvéole maximale est de 50 µm/0,001969".
Pour les saillies/bosses, le nombre reste le même pour tout diamètre de microvia plaqué fermé avec un maximum de saillies/bosses de 25 µm/0,000984.
Il est important de noter que le tableau 3-14 s'applique uniquement aux microvias dans les emplacements destinés à être soudés lors de l'assemblage. Dans tous les autres emplacements de microvias qui ne sont pas destinés à être soudés lors de l'assemblage, les saillies et les creux ne sont pas rejetables lorsque toutes les autres conditions sont remplies.
Si des conditions de finition plus strictes sont requises, veuillez documenter votre AABUS (Conformément à l'accord entre l'utilisateur et le fournisseur) sur votre documentation d'achat. Pour une meilleure pratique, veuillez ajouter votre exigence sur le plan de fabrication.
Restez à l’écoute des autres changements apportés à la norme IPC-6012 rev F de Summit Interconnect.
Voici une photo d'un microvia avec une fossette.
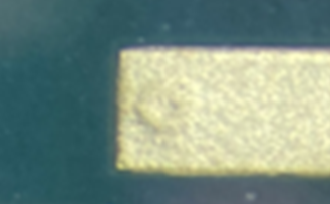
Et un avec une saillie.
Pour toute question complémentaire sur les modifications apportées à la révision F de l'IPC-6012 ou pour toute question technique, Summit Interconnect est là pour vous aider. Envoyez un e-mail à notre équipe d'ingénierie des applications sur le terrain à l' adresse fae@summitinterconnect.com .