La demande croissante de circuits imprimés (PCB) miniaturisés à haute densité d'interconnexion (HDI) a fait des microvias indispensables pour obtenir des conceptions compactes et performantes. Cependant, la conception de circuits imprimés avec microvias Placés sur des vias mécaniques remplis d'époxy et recouverts d'un revêtement, ces dispositifs présentent des défis de fiabilité importants. Cet article examine les mécanismes de défaillance sous-jacents, propose une explication détaillée des problèmes critiques et présente des stratégies pour améliorer la fiabilité de ces structures.
Introduction
Les microvias sont essentiels à la connectivité intercouche des circuits imprimés HDI, permettant des configurations compactes et des fonctionnalités avancées dans l'aérospatiale, l'automobile, les télécommunications et d'autres secteurs à haute fiabilité. Cependant, les microvias percés dans le revêtement des vias mécaniques remplis d'époxy sont particulièrement vulnérables aux défaillances mécaniques, thermiques et d'adhérence. La résolution de ces vulnérabilités nécessite une compréhension de leurs causes profondes et la mise en œuvre de stratégies de conception et de fabrication robustes.
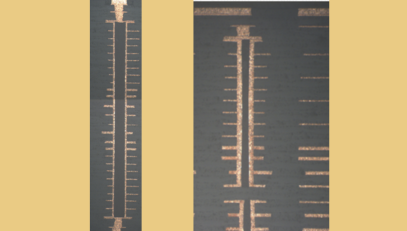
Mécanismes de défaillance
1. Contrainte mécanique au niveau du revêtement du capuchon
Le revêtement de protection, une fine couche de cuivre scellant le via rempli d'époxy, est sujet à des faiblesses structurelles, en particulier lorsqu'il est soumis à des contraintes de perçage ou de fonctionnement.
- Placage mince et faiblesse structurelle : le placage du capuchon est généralement plus fin que les parois en cuivre des vias standard, ce qui limite sa capacité à résister aux contraintes mécaniques, notamment celles dues au perçage au laser.
- Contraintes localisées dues au perçage de microvias : le perçage de microvias dans le revêtement de protection introduit des contraintes mécaniques et thermiques localisées. Même un perçage laser précis peut laisser des microfissures ou des bords irréguliers qui agissent comme des concentrateurs de contraintes.
- Support mécanique insuffisant de l'époxy : Contrairement au cuivre massif, l'époxy ne possède pas la rigidité mécanique nécessaire pour renforcer le revêtement de protection. Par conséquent, le revêtement de protection supporte la majeure partie de la charge mécanique, ce qui augmente sa sensibilité à la déformation et à la fissuration.
2. Inadéquation de la dilatation thermique
Les cycles thermiques pendant le soudage, les tests et le fonctionnement imposent une contrainte considérable sur le placage du capuchon et l'époxy en raison des différences dans leurs propriétés matérielles.
- Différents coefficients de dilatation thermique (CTE) : le cuivre et l'époxy se dilatent à des vitesses différentes sous l'effet de la chaleur. Le CTE plus élevé de l'époxy crée des contraintes de traction dans le revêtement du capuchon lors des excursions thermiques.
- Fissuration par fatigue : les cycles thermiques répétés affaiblissent le revêtement du capuchon, provoquant des microfissures qui se propagent dans le microvia ou le noyau époxy.
- Points chauds localisés : les microvias sur les vias plaqués capuchon entravent la dissipation de la chaleur, créant des points chauds qui exacerbent le stress thermique et accélèrent la graisse du matériau.
3. Problèmes d'adhérence entre l'époxy et le cuivre
L'interface entre le remplissage époxy et le placage du capuchon est un point de défaillance courant en raison d'une liaison faible, qui découle de la nature du processus de placage au cuivre autocatalytique.
- Époxy autocatalytique sur cuivre durci : une fois l'époxy durci et planarisé, la surface devient lisse et ne présente ni microrugosité ni promoteurs d'adhérence présents dans les feuilles de cuivre standard. Le cuivre autocatalytique déposé sur cette surface lisse présente une résistance au pelage intrinsèquement inférieure à celle des feuilles de cuivre.
- Absence de promoteurs d'adhérence : les feuilles de cuivre contiennent généralement des promoteurs d'adhérence (tels que des traitements d'oxyde ou de réduction d'oxyde) pour améliorer la liaison avec le substrat sous-jacent. Ces promoteurs créent une interface mécaniquement imbriquée, augmentant considérablement la résistance au pelage. En revanche, le cuivre chimique repose uniquement sur l'adhésion chimique, qui est moins robuste.
- Délaminage sous contrainte : La liaison plus faible entre le cuivre chimique et l'époxy planarisé augmente le risque de délaminage lorsqu'il est soumis à des charges mécaniques ou thermiques. Ce délaminage crée des sites d'initiation de fissures, réduisant à la fois l'intégrité structurelle et la connectivité électrique.
4. Vulnérabilités spécifiques à Microvia
Les microvias percés dans le revêtement de protection sur des vias remplis d'époxy sont confrontés à des défis uniques qui compromettent leur fiabilité :
- Fondation inadéquate : les microvias nécessitent une fondation en cuivre solide et continue pour la stabilité et la répartition des contraintes. L'époxy plus souple sous le revêtement de protection ne parvient pas à fournir un support mécanique adéquat.
- Amplification des contraintes aux interfaces : Le point de transition entre la paroi du microvia et le revêtement du capuchon subit une concentration de contraintes, ce qui en fait un point chaud pour l'initiation et la propagation des fissures.
- Propagation des fissures dans les microvias : les microfissures provenant du revêtement du capuchon s'étendent souvent dans les parois des microvias, menaçant la continuité électrique et la stabilité structurelle.
5. Défauts de vide et de placage
Les défauts dans le remplissage époxy ou le placage du capuchon aggravent les problèmes de fiabilité.
- Vides dans le remplissage époxy : le piégeage de gaz ou un durcissement irrégulier crée des vides qui affaiblissent les performances mécaniques et thermiques de la via.
- Placage de capuchon incohérent : un dépôt de cuivre irrégulier ou mince sur des vias remplis d'époxy introduit des points faibles susceptibles de se fissurer sous contrainte.
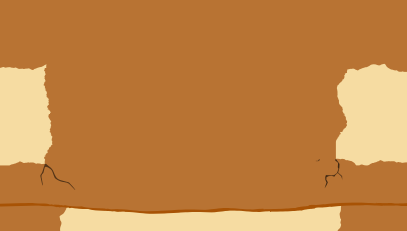
Conséquences des échecs
L’interaction de ces mécanismes de défaillance conduit à plusieurs effets néfastes :
- Discontinuité électrique : les fissures sectionnent les voies conductrices, provoquant une perte de signal ou des circuits ouverts.
- Problèmes de dissipation thermique : une conductivité thermique réduite affaiblit la dissipation thermique, créant une surchauffe localisée.
- Fatigue accélérée : la concentration des contraintes et les inadéquations des matériaux amplifient la fatigue, réduisant ainsi la durée de vie opérationnelle du PCB.
Stratégies d’atténuation
1. Pratiques de conception sûres
- Vias décalés : évitez de placer des microvias directement sur des vias remplis d'époxy pour répartir les contraintes plus uniformément.
- Tampons en forme de larme : utilisez des tampons en forme de larme au point d'entrée du microvia pour réduire la concentration de contraintes.
2. Matériaux et structures améliorés
- Vias remplis de cuivre : remplacez les vias remplis d'époxy par des alternatives remplies de cuivre pour fournir une base conductrice robuste.
Époxy adapté au CTE : utilisez des matériaux époxy avec un CTE inférieur pour minimiser les décalages de dilatation thermique. - Placage de capuchon plus épais : augmentez l'épaisseur du placage de capuchon pour améliorer la résistance mécanique et thermique.
3. Optimisation des processus
- Remplissage sans vide : utilisez des techniques avancées pour garantir un remplissage et un durcissement uniformes de l'époxy, éliminant ainsi les vides.
- Qualité de placage constante : maintenez un contrôle de qualité rigoureux pour garantir un placage uniforme des capuchons.
4. Tests et inspections avancés
- Essais thermiques et mécaniques : valider la fiabilité dans des conditions opérationnelles simulées, telles que les tests de cyclage thermique et de vibration.
- Techniques d’inspection : Utiliser l’imagerie par rayons X et l’analyse transversale pour détecter les vides, le délaminage ou d’autres défauts.
Conclusion
Le placement de microvias sur des vias mécaniques remplis d'époxy et recouverts d'un revêtement métallique présente de nombreux défis qui compromettent la fiabilité des circuits imprimés. Comprendre les causes profondes de ces défaillances (contraintes mécaniques, décalages thermiques et faible adhérence) permet aux ingénieurs de concevoir des circuits imprimés HDI plus robustes. L'utilisation de matériaux avancés, de configurations de vias optimisées et de contrôles de fabrication rigoureux permet d'améliorer la durabilité et les performances de ces structures d'interconnexion critiques.
Références
- IPC-6012 : « Spécification de qualification et de performance pour les circuits imprimés rigides. »
- IPC-2226 : « Norme de conception pour les cartes de circuits imprimés à interconnexion haute densité (HDI) ».
- Park, J. et Yoo, C. (2019). « Modes de défaillance des structures à microvias soumises à des cycles thermiques ». Transactions IEEE sur les composants, l'emballage et la technologie de fabrication.
- Phan, T., et Wright, T. (2020). « Améliorer la fiabilité des microvias grâce à l'optimisation des matériaux et des procédés. » Conception et fabrication de circuits imprimés.
- Bhattacharya, S. (2017). « Techniques de fabrication avancées pour les circuits imprimés HDI ». Journal des technologies de fabrication électronique.