Conception PCB : Bague annulaire plaquée à travers le trou Classe 2, Classe 3 et Tangence « Classe 3 légère ».
Ce que les concepteurs doivent savoir pour maintenir les exigences minimales en matière de bagues annulaires. Cet article présente, du point de vue du fabricant, les meilleures pratiques pour réussir la première révision conformément aux exigences IPC-6012 et aux directives de conception IPC-2221.
Contexte : Cet article vise à aider les concepteurs de circuits imprimés à comprendre les différences entre le diamètre de perçage réel et la taille du trou fini spécifiée sur le plan de fabrication, ainsi que son impact sur l'anneau requis pour la fabrication d'un circuit imprimé conforme. Il présente également les meilleures pratiques pour documenter les vias et les trous métallisés des composants, afin d'indiquer clairement les exigences finales, tout en offrant au fabricant de circuits imprimés la plus grande latitude pour assurer la conformité avec le rendement le plus élevé possible.
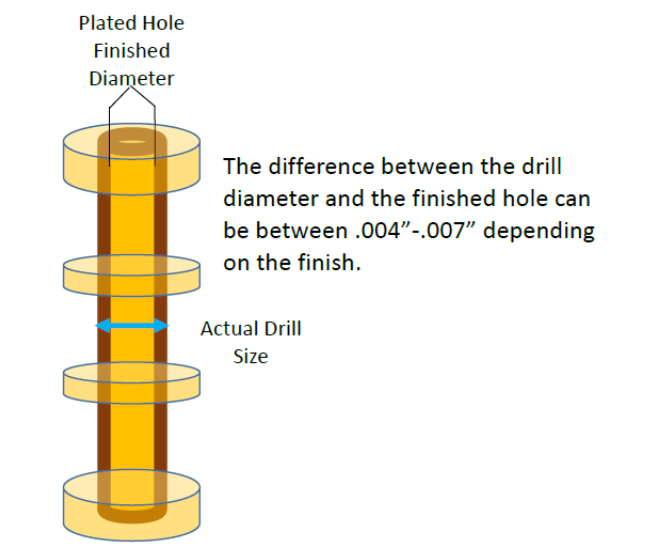
Commençons par les bases : « Qu'est-ce qu'une bague annulaire ? » La définition d'une bague annulaire diffère selon qu'il s'agit de couches externes ou internes. Pour les couches externes, la bague annulaire minimale correspond à la distance minimale entre l'intérieur d'un trou métallisé fini et la distance la plus courte sur la surface de la couche externe.
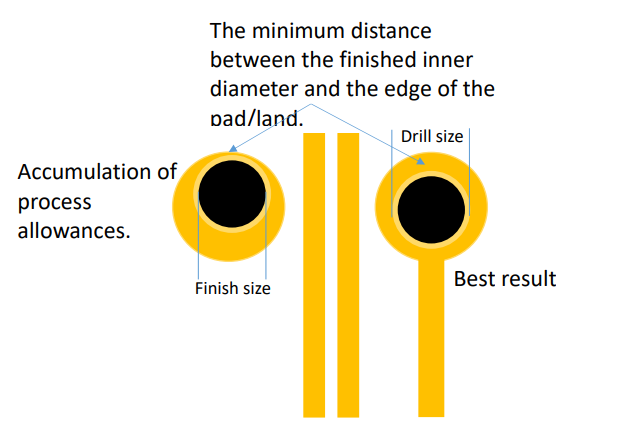
La bague annulaire de la couche intérieure est déterminée en fonction du diamètre du foret et de la distance la plus courte jusqu'au bord de la zone forée. La taille des trous finis n'est pas prise en compte.
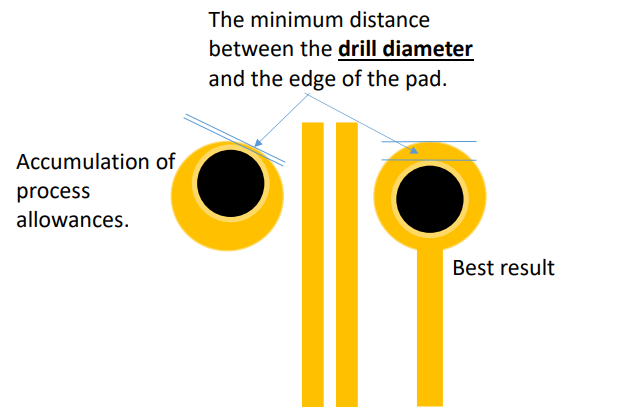
Maintenant que nous avons examiné les différences observables entre les bagues annulaires extérieures et intérieures, examinons le tableau 3-9 de la révision E de l'IPC-6012.
La bague annulaire minimale autorisée pour la couche externe de classe 3 est de 0,001969 po mesurée à partir du diamètre intérieur du trou plaqué fini jusqu'au bord le plus court de la plage plaquée.
La bague annulaire minimale autorisée pour la couche interne de classe 3 est de 0,000975 po et est mesurée à partir du diamètre du foret jusqu'à la distance la plus courte jusqu'au bord du terrain.
La classe 2 autorise une rupture à 90 degrés à condition qu'il y ait une déchirure, un filetage ou un trou de serrure à la jonction du conducteur de terre. Voici une illustration expliquant ce qui est autorisé et ce qui est requis.
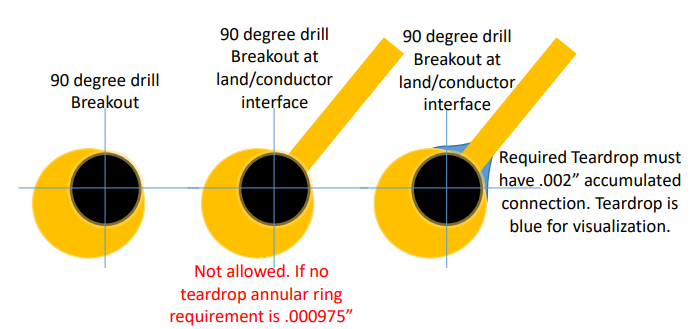
Avec l'augmentation des densités, de nombreuses conceptions de classe 3 ne peuvent atteindre un diamètre annulaire minimal de 0,000975 pouce, ni accepter des dérivations à 90 degrés pour une fiabilité élevée. Une solution intéressante consiste à autoriser la tangence, à condition d'ajouter des gouttes à l'interface méplat/conducteur.
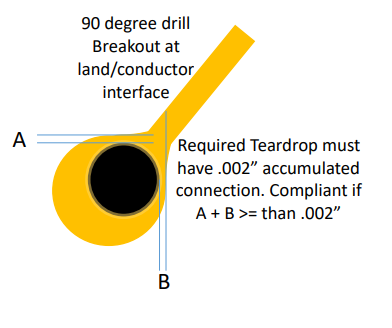
Plusieurs de mes clients appellent affectueusement la tangence « Classe 3 légère ». À l'heure actuelle, cette condition n'est pas classée pour les trous métallisés mécaniques dans les normes IPC[1]6012 et IPC-A-600. Si vous choisissez cette option pour votre conception, vous devrez préciser cette tolérance. Cette condition est appelée condition AABUS (Conformément à l'accord entre l'utilisateur et le fournisseur).
La deuxième partie de cet article vise à aider les concepteurs à déterminer la taille de la bague annulaire nécessaire. Cette valeur dépend de la complexité de la conception. Je recommande aux concepteurs de consulter la section 9.1.1, la section 9.1.2 et le tableau 9-1 de la norme IPC-2221.
En tant que concepteur, si un fabricant vous a déjà appelé et vous a informé que la conception ne comporte pas suffisamment de bague annulaire pour être conforme, cette section vous aidera à comprendre pourquoi le fabricant exige une bague annulaire adéquate alors qu'il semble qu'il y en ait suffisamment actuellement dans la conception.
Pour commencer, l'enregistrement d'un foret et des terres sur toutes les couches n'est pas un processus parfait. Voici une description simple des tolérances de traitement et de leur raison d'être.
- Le matériau époxy tissé que nous achetons varie d'un lot à l'autre. Cette variation est généralement d'environ +/- 0,0002 po par pouce. Si vous reportez cette valeur à la surface de travail d'un panneau de production, vous constaterez une variation de 0,0025 po de chaque côté du panneau.
- L'enregistrement d'avant en arrière d'un système moderne d'imagerie directe laser est généralement de 0,001".
- La précision du poinçonnage post-gravure d'un noyau gravé est de 0,001" au mieux.
- Le laminage et l'outillage ajoutent 0,001 po de tolérance supplémentaire.
- Le tableau 9-1 de l'IPC-2221 fournit des conseils pour augmenter la bague annulaire de 0,001 po si le nombre de couches est supérieur à 8.
- La position zéro de la perceuse et la précision de la course du foret peuvent ajouter 0,001 po de plage de tolérance accrue.
- Les forets peuvent se déplacer. La couche supérieure percée est précise, mais tout déplacement du foret aura un impact sur les couches inférieures de l'empilement.
- Les constructions à sous-laminage multiples ajouteront une tolérance supplémentaire de 0,002 po lorsque plusieurs structures à sous-laminage sont laminées dans l'assemblage final.
Veuillez noter que les valeurs suivantes sont basées sur le diamètre réel du foret et NON sur la taille du trou FINI.
En examinant les valeurs de processus cumulées, nous divisons la tolérance par deux. Cette valeur peut être divisée par deux puisque nous répartissons l'erreur entre les panneaux de production. Ainsi, si nous additionnons toutes les valeurs pour un cycle de laminage unique à nombre de couches élevé, la tolérance de processus peut atteindre 0,0045 po pour la tangence. Si le travail comporte plusieurs cycles de laminage, la tolérance de tangence serait de 0,006 po pour le perçage final.
Si vous envisagez une classe 3, la valeur de la bague annulaire augmentera de 0,001 pouce supplémentaire. Pour un cycle de laminage unique, nous demandons généralement une bague annulaire de 0,006 pouce. Pour plusieurs cycles de laminage, nous autorisons une bague annulaire de 0,006 pouce pour le premier cycle de sous-laminage, mais nous demandons une bague annulaire de 0,007 pouce pour les cycles de laminage suivants.
Le dernier élément que les concepteurs doivent prendre en compte est la largeur de perçage réelle du foret par le fabricant. Pour répondre à cette question, il serait utile que le concepteur dispose de deux règles. Une pour les vias plaqués dans lesquelles la taille du trou fini n'a pas d'importance, et deux tailles de trous de composants qui ont généralement une avance dans le trou plaqué fini. Les trous de composants doivent indiquer la taille du trou fini et la tolérance autorisée.
Les vias doivent être indiqués comme tels et la taille du trou fini peut être inférieure à la taille de perçage spécifiée. La plupart des conceptions indiquent la taille de via qui correspond à la taille réelle du foret que le fabricant doit utiliser. L'utilisation de la taille réelle du foret permettra d'obtenir la bague annulaire correcte et une distance de sécurité « sûre » entre un foret et un autre filet. Pour indiquer clairement qu'un foret particulier est un via, le concepteur doit utiliser la tolérance suivante dans le tableau de perçage.
Cet exemple utilise une traversée de 0,010 po. Foret x 0,010 po + 0,002 po/- diamètre de foret.
Cette instruction indique clairement au fabricant que le concepteur suppose que la conception a été configurée et vérifiée avec un foret de 0,010 po. Un fabricant peut examiner cette exigence et déterminer quel foret fournira les meilleurs rendements tant que le trou fini est de 0,012 po ou moins. Dans certains cas, un fabricant percera plus grand s'il y a beaucoup d'anneaux annulaires, ou il peut choisir de percer plus petit pour s'assurer que la pièce finie aura des anneaux annulaires conformes.
Trous de composants. Ces valeurs peuvent varier d'un fabricant à l'autre. Pour les trous de composants, le fabricant doit compenser la taille du foret pour le placage et les variations de taille du trou une fois tous les processus de fabrication terminés. Voici des valeurs typiques à prendre en compte lors des vérifications DRC en CAO.
Finitions d'immersion ENIG, ENEPIG ou Silver, la taille du foret est de 0,004" plus grande que la taille du trou fini.
La soudure à air chaud (HASL) permet de terminer le perçage avec une taille de trou de 0,006 po supérieure à celle du trou fini. Le refroidissement de la soudure à air chaud est irrégulier et le trou fini est obstrué.
La plaque de refusion en étain-plomb peut être percée de 0,007 po de plus que le trou fini. Lors du processus de refusion, cela peut obstruer le trou plus que HASL.
Si une épaisseur de placage de trou plus élevée est requise, il sera nécessaire d'augmenter le diamètre du foret de fabrication pour répondre à l'exigence de placage supplémentaire.
Résumé : J'espère que ces informations vous seront utiles pour vos futures conceptions, sans problèmes qui seraient autrement détectés chez le fabricant. Mon objectif est d'aider les concepteurs à obtenir des conceptions sans erreur, de leur système de CAO à nos systèmes de FAO, sans détection de DRC.
Pour mémoire, cet article s'appuie sur la gestion du département d'ingénierie d'un fabricant pendant plus de 20 ans et près de 40 000 conceptions différentes. Summit Interconnect fabrique des produits de R&D de pointe avec des forets de 0,004 pouce de diamètre dans des zones de 0,0097 pouce et des produits de classe 3 pour l'aéronautique et l'espace.
Voilà, c'est tout. Vos questions et/ou suggestions sont les bienvenues. Si vous avez une question sur la fabrication de PCB à laquelle vous aimeriez obtenir une réponse, veuillez envoyer vos questions à mon compte LinkedIn.
Restez en bonne santé et en sécurité, tout le monde !