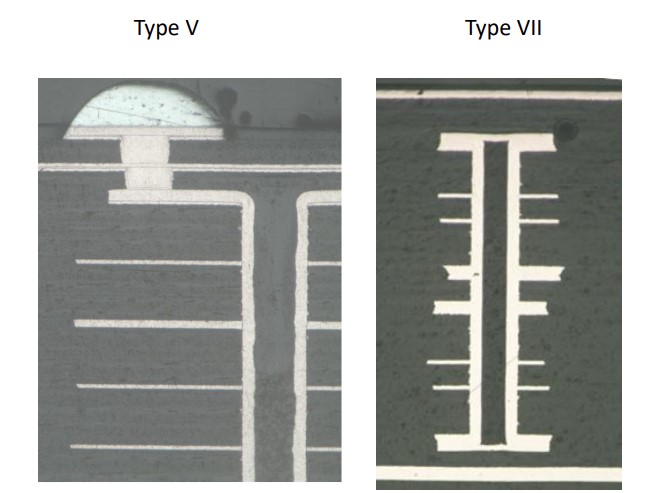
Les deux structures présentent des vias enterrés, mais le type V de gauche n'est pas recouvert de cuivre, tandis que celui de droite est recouvert de cuivre époxy. Notez l'épaisseur de cuivre plus importante sur le type VII que sur le type V. Grâce à cette réduction de cuivre, nous obtenons les résultats suivants :
- Le cuivre de base plus fin de type V permet un espacement plus fin.
- Le type V comporte 20 à 25 étapes de traitement en moins, ce qui peut réduire les temps de cycle de 1 à 3
jours. - Si le type VII est invoqué, l'absence de revêtement de protection est considérée comme non conforme.
- Si le type VII est invoqué, une fossette profonde supérieure à celle autorisée par le tableau 3-11 de l'IPC-6012 serait considérée comme non conforme.
- Si le type VII est invoqué, un placage de capuchon inférieur à celui autorisé par le tableau 3-11 de l'IPC-6012 sera considéré comme non conforme.
Le type V ne répond à aucune des trois dernières exigences, ce qui garantit une conformité accrue grâce à un processus moins complexe. La base de cuivre réduite réduit les courts-circuits et assure des rendements plus élevés.
La définition et le but du type V :
Ces informations sont disponibles dans la section 5.5 et le tableau 5-1 de la norme IPC-4761. Section 5.5 « Un via avec un matériau appliqué dans le via visant une pénétration et une encapsulation complètes du trou. La section 5.5 et le tableau 5-1 indiquent tous deux que le type V est bénéfique pour « être utile dans le processus de lamination séquentielle ». Il indique le même avantage pour le type VII, mais il n'y a aucune explication sur ce que c'est pour le type V ou VII.
Voici les avantages du type V.
- Avantage 1 La base inférieure en cuivre permet un espace conducteur plus petit :
- Le type V ne nécessite pas de placage par enroulement (si vous ne connaissez pas cette technique et que vous avez un via dans le pad ou un remplissage époxy de légende, veuillez consulter la section 3.6.2.11.1 de l'IPC-6012). Le placage par enroulement standard augmente le cuivre de base des couches extérieures percées dans la structure enterrée. L'épaisseur du placage par enroulement peut varier au cours du processus et un espace accru est nécessaire pour la gravure. Le type V ne nécessite pas ce processus, de sorte que le cuivre de base reste au niveau du cuivre de départ et permet un espace plus fin avec les meilleurs rendements. La plaque à motifs des couches enterrées extérieures plaquera naturellement le cuivre qui s'enroule du via sur les couches enterrées extérieures.
- Avantage 2 Moins d'étapes de processus Temps de cycle plus rapide :
- Les constructions de type V réduisent le processus de fabrication de PCB de 20 à 25 étapes. La structure enterrée est laminée, percée, préparée, électrolytiquement, puis gravée et remplie d'époxy. Veuillez noter que le remplissage s'effectue après la gravure du motif de la couche extérieure de la structure enterrée. Cette étape est suivie de la structure de laminage suivante.
- Avantage 3 Le plus important Les trous vias remplis après la gravure empêchent la perte de résine dans les vias.
- Si les vias enterrés n'étaient pas remplis, la résine du préimprégné issue du cycle de laminage suivant serait expulsée du verre tissé et s'infiltrerait dans les vias enterrés ouverts. Cette perte de résine pourrait conduire à une situation dangereuse dans laquelle la résine serait « affamée » du tissage entre le sous-ensemble enterré et la couche suivante (généralement la feuille de la couche extérieure). Le manque de résine pourrait permettre à l'humidité de pénétrer dans le diélectrique extérieur, ce qui pourrait entraîner un événement de délaminage pendant l'assemblage ou l'application de HASL (Hot Air Solder Level). Le remplissage de type V empêche la perte de résine et protège le PCB fini de la condition de manque de résine.
- Le type V ne requiert pas d'exigences de type VII qui sont considérées comme non conformes. Exemple d'une via de type V qui répond à l'exigence.
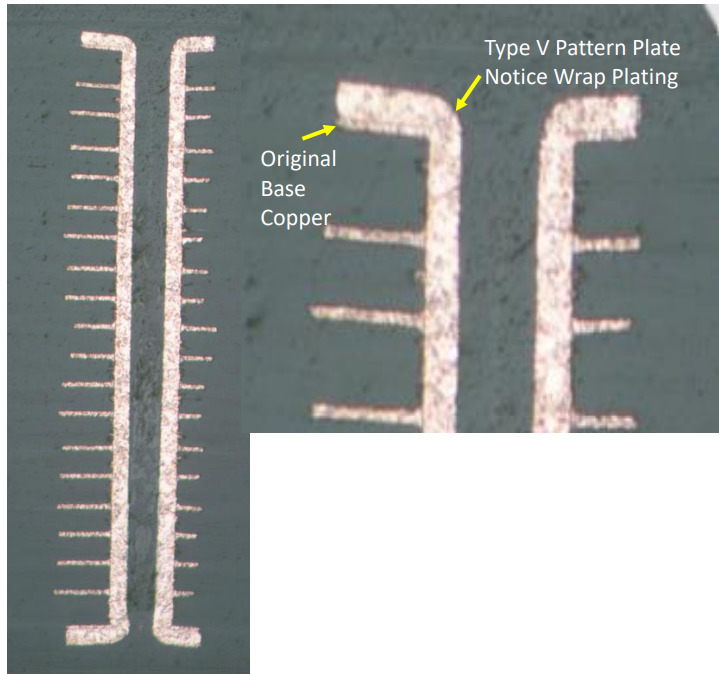
La définition et le but du type VII :
Comme indiqué précédemment, le type VII présente les mêmes avantages que le type 5. La définition du type VII se trouve dans la section 5.7 de l'IPC-4761.
Avantages supplémentaires :
- Via dans Pad, mais il s'agit d'une structure via enterrée. Il n'y a donc aucun avantage à ce que la structure via soit enterrée.
- Empilement de vias : À éviter ! Un microvia sur un via enterré de type VII est susceptible de tomber en panne dans presque tous les cas. ÉLOIGNEZ LE MICROVIA DU TYPE VII.
Exigences pour le type VII qui ne bénéficient pas d'une via enterrée :
- Le plaquage de protection est une exigence superflue, car une via enterrée est enterrée. Cependant, un inspecteur rejettera une commande si le plaquage de protection est manquant et que la via enterrée est spécifiée comme étant de type VII ou plaquage de protection.
- Le placage par enrobage, requis pour les circuits de type VII, est indispensable à la fiabilité. Dans ce cas, nous visons une épaisseur minimale de 200 ou 500 micropouces, et une fenêtre cible de 400 micropouces. Cela augmente évidemment la difficulté et nécessite que la conception prévoie suffisamment d'espace pour le cuivre d'enrobage ajouté sur le cuivre de base. Après le placage, le fabricant doit graver le cuivre de base d'origine et le cuivre plaqué par enrobage ajouté. La variation de l'épaisseur du placage par enrobage ajoute à la complexité. Cela peut entraîner des variations de hauteur et de largeur des conducteurs sur les couches externes enterrées. Si vous êtes ingénieur en RF ou en intégrité du signal, vous n'apprécierez probablement pas cette variante.
- La profondeur maximale autorisée est de 0,003 po pour la classe 3 et de 0,005 po pour la classe 2. Si un inspecteur à la source détecte une profondeur supérieure à ces valeurs, elle sera considérée comme non conforme. Si le type V ou VII présentait une profondeur de 0,010 po, elle pourrait facilement être comblée avec du préimprégné issu du cycle de laminage suivant, sans créer de manque de résine.
Via enterrée de type VII (simple conforme)
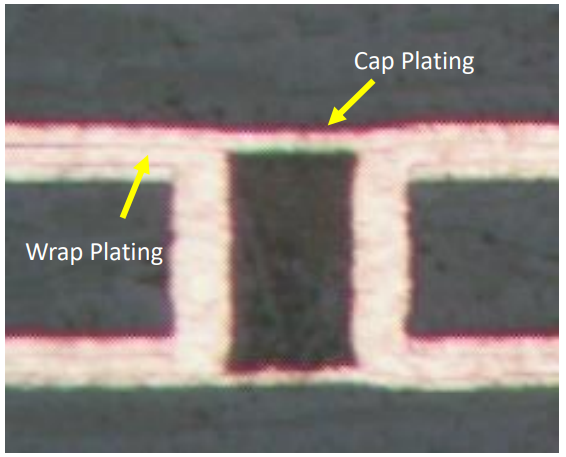
Type VII qui ne sont pas conformes mais qui répondent aux exigences de forme et de fonction, et qui, s'ils étaient définis comme Type V, auraient été acceptables.
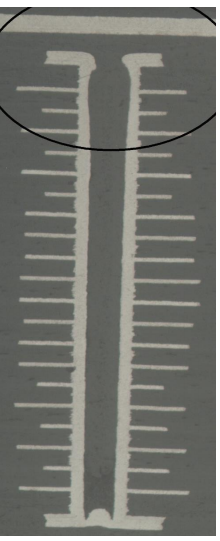
Voici une condition dans laquelle le type VII était requis et une condition de non-conformité s'est produite, mais si le type V était autorisé, cette condition ne se serait pas produite.
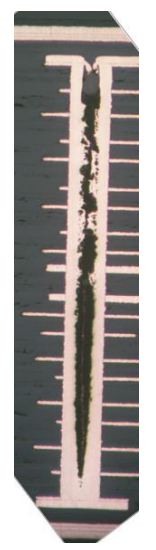
Voici les résultats du test OM d'un travail de via enterré avec des vias de type V.
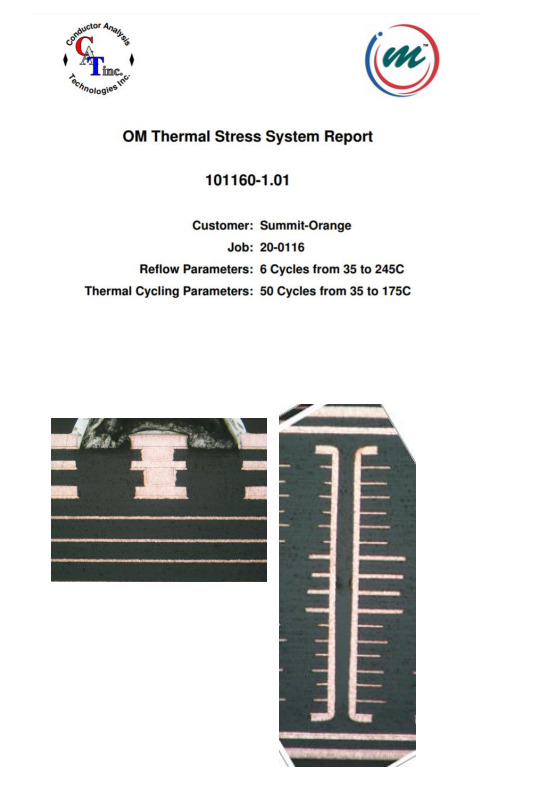
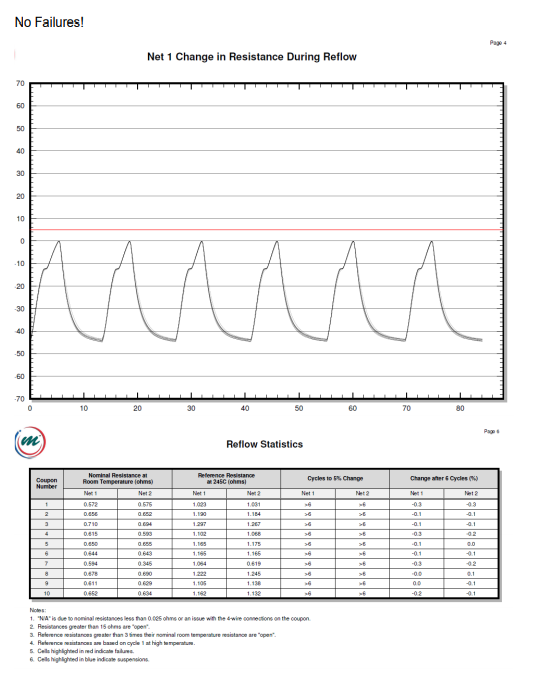
En résumé:
Les conceptions HDI qui ont des vias enterrés bénéficieront de la spécification IPC-4761 Type V au lieu du Type VII.
- Temps de cycle réduits permettant d'économiser 1 à 3 jours dans la fabrication des PCB
- Espacement des conducteurs inférieur. Généralement de 0,0005 à 0,001 pouce inférieur.
- Des rendements de fabrication plus élevés se traduisent par une meilleure livraison dans les délais et en quantité totale.
- Moins de conditions non conformes et de demandes de dérogations de conformité.
- Épaisseur constante du conducteur
Il existe peu de cas où l'ingénieur (performances de signal constantes), le concepteur (fonctionnalités plus petites) et le fabricant (temps de cycle plus court et rendements plus élevés) bénéficient tous de la même pratique. Merci d'avoir écouté les commentaires d'un fabricant !